Sakthi Sugars Limited is one of the largest producers of
white crystal sugar in the country accounting for a
capacity of 16,500 tons of cane crush per day (TCD).
In coherence with Sakthi Sugars' continued effort to
enhance the efficiency of production many initiatives have
been put to practice time and again to enrich the quality
of production process to unmatched standards. Some such
initiatives are listed below,
- Scientific farming.
-
Continuous R&D in sugar rich, pest resistant and high
yielding sugarcane varieties.
- Mechanization of cane harvesting.
-
Efficient Sugar manufacturing process to reduce sugar
loss.
-
Ensuring cleanliness and hygiene at their best in
factory sites.
- Auto Setting Mill facilities.
-
Energy Saving Schemes like planetary gear boxes,
Automated cooling and condensing system, vertical
continuous pan, etc.,
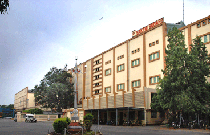
The Sakthinagar Unit, a pioneer that introduced Mechanical
Cane Harvester in the country, was established in the year
1964 at Sakthinagar in Erode District, Tamil Nadu with an
initial capacity of 1250 TCD, scaling higher in stages,
today, the Unit has consolidated its growth with an
aggregate capacity of 9000 TCD.
The Unit is strategically placed in terms of its location.
It is situated in the most favorable climatic zone of the
country that hosts more than 35,000 acres of sugarcane
cultivation, well irrigated by Rivers and Canals.
Nonetheless benchmarking its own records and operating all
365 days in an year , the Sakthi Nagar unit has recorded
the highest cane crush of 22.35 Lakh M.T during 2006 –07
seasons. The plant achieved more than 1000 days of
continuous cane crushing during 2004-07. With its
excellence to repeat its success stories, the Unit has won
the National Award for Exemplary Export Performance and
has also won National Efficiency Award for many years. The
Unit also has the distinct capacity of Raw Sugar
Processing to produce high quality sugar using
conventional equipments.
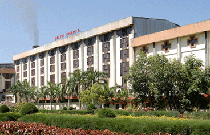
It was established in the year 1988 – 89 at Padamathur in
Sivaganga District, Tamilnadu. It has an advanced
infrastructure equipped with Auto Setting Mills and the
technical know-how to process Raw Sugar.
The plant which was begun with a capacity of 2500 TCD has
expanded to 4000 TCD. The plant recorded the highest cane
crush of 10 Lakh MT in the 2007-08 Season.
The plant features
-
State-of-the-art automatic syrup clarification and
melt clarification systems to produce low ICUMSA
colour sugar.
-
Modern Fluidised Bed Drier for sugar drying and most
modern sugar grader.
A pioneer
-
The Sivaganga Plant is a pioneer in introducing
planetary gear Box
and in designing silo, a mechanical device for raw
sugar handling at Ports and Jumbo Bags of 2 tons
capacity.
-
It showed the industry that the entire sugarcane
cultivation can be brought under total
mechanization.
-
The Plant introduced large scale sub surface drip
irrigation system for sugarcane crop facilitating
mechanized cultivation and harvesting.
-
It was the first one to install Vertical
continuous PAN and to have operated it
successfully in India.
(The Vertical continuous PAN operates at very low
vapor pressure & Temperature)
Some of the measures adopted by the Unit for energy
conservation include.
- Use of AC Variable frequency drives.
-
Use of energy saving equipments in process like
flash steam recovery, direct contact heaters, vapour
line juice heaters, dynamic juice heaters and
automated single entry multi jet condensers etc.,
The unit indigenously designs and develops farm
implements viz., modified tumkur plough, Disc off
Barrer, Roto Incorporator, ridgers for earthing up,
Sakthi drip laying machine.
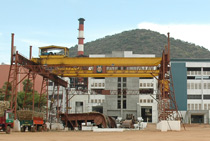
The plant with the capacity of 3500TCD was instituted in
the year 2007 at Poondurai Semur in Erode
District,Tamilnadu.
In the Trial Season during 2007 the Unit crushed 711609 MT
of Cane with an average recovery of 9.11 % which is a rare
feat and a remarkable achievement in the national level.
Subsequently it produced a laudable quantum of 1.21 Lakh
qtls of 45 ICUMSA sugar which was exported.
The Unit also introduced Decanters for removing impurities
from the juice as against Vacuum filters and also
installed energy saving equipments to minimize steam
consumption and loss.